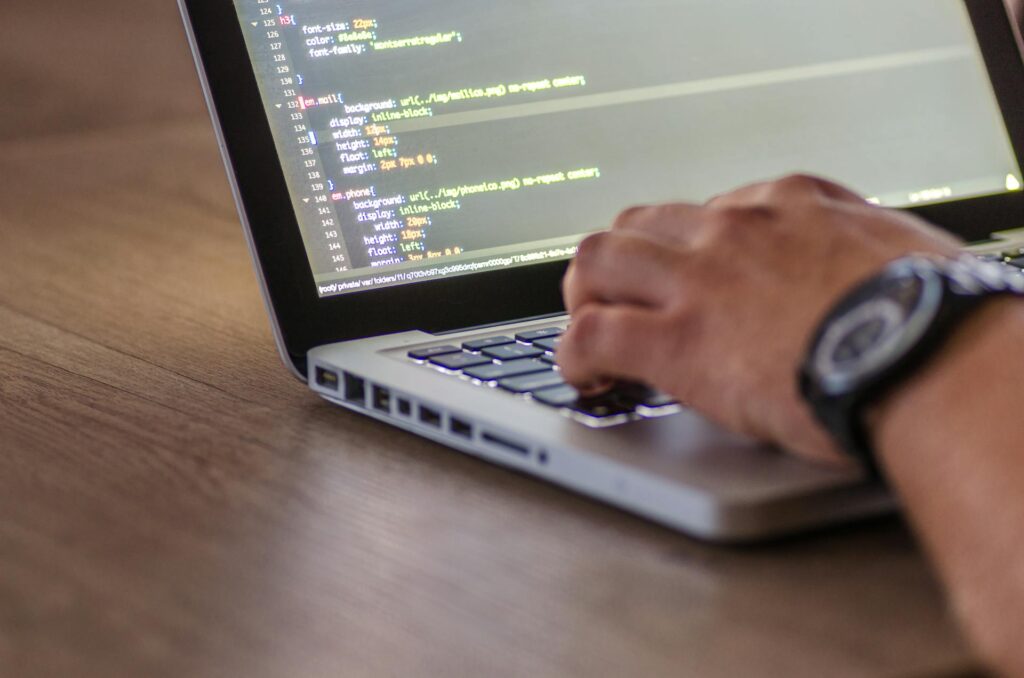
Product defects are a serious problem for companies throughout industries. Whether or not in manufacturing, electronics, or shopper items, defects result in elevated prices, dissatisfied prospects, and harm to model status. Even with stringent high quality management processes, many firms nonetheless battle with defects that slip by means of manufacturing. These points not solely impression profitability but additionally trigger provide chain disruptions and regulatory compliance challenges.
Widespread Causes Companies Wrestle with Product Defects
1. Inconsistent Manufacturing Processes
Manufacturing includes a number of steps, from uncooked materials processing to remaining meeting. If these processes lack standardization, defects turn out to be inevitable. Variations in gear settings, operator ability ranges, and materials high quality can result in inconsistencies that have an effect on the ultimate product. With out strict course of management, minor deviations can accumulate, leading to faulty models that require rework or scrapping.
2. Human Errors in High quality Management
High quality management groups are chargeable for figuring out defects earlier than merchandise attain prospects, however guide inspections usually are not foolproof. Human fatigue, oversight, and restricted inspection time make it troublesome to catch each defect. Moreover, when manufacturing volumes are excessive, high quality checks turn out to be rushed, growing the chance of faulty merchandise being shipped. Companies relying solely on guide high quality management usually battle to take care of constant product high quality.
3. Poor Provider High quality Administration
Many firms supply uncooked supplies and elements from third-party suppliers. If suppliers fail to satisfy high quality requirements, defects can enter the manufacturing line undetected. Inconsistent provider high quality results in variations in product efficiency, elevated rework, and better return charges. With out an efficient provider administration system, companies face challenges in guaranteeing uniformity throughout manufacturing batches.
4. Lack of Actual-Time Monitoring
Defects usually go unnoticed till later levels of manufacturing and even after merchandise are within the arms of consumers. Delayed defect detection results in expensive recollects, guarantee claims, and broken buyer belief. Companies that lack real-time monitoring programs battle to determine defects early, making corrective actions reactive slightly than preventive.
5. Insufficient Information Utilization
Many companies gather giant volumes of manufacturing information however fail to make use of it successfully. With out superior analytics, figuring out patterns in defect occurrences turns into troublesome. Corporations that depend on outdated reporting strategies miss helpful insights that would assist enhance manufacturing processes and scale back defects.
How Software program Can Assist Companies Cut back Product Defects
1. Automated High quality Management and Inspection
AI-powered defect detection software program eliminates human error by automating high quality inspections. Machine imaginative and prescient programs geared up with deep studying algorithms can analyze merchandise in real-time, figuring out defects that human inspectors may overlook. These programs scan hundreds of models per minute, guaranteeing the next stage of accuracy and consistency.
Automated high quality management software program additionally integrates with current manufacturing gear, permitting for real-time defect detection at completely different manufacturing levels. By catching defects early, companies can stop defective merchandise from transferring additional down the provision chain, decreasing rework prices and bettering total effectivity.
Furthermore, producers can enhance design accuracy through the use of tolerance evaluation software program to make sure that elements match collectively appropriately, decreasing the possibilities of defects brought on by dimensional variations.
2. Predictive Analytics for Defect Prevention
Predictive analytics software program makes use of historic manufacturing information and machine studying fashions to anticipate defect tendencies. By analyzing previous defect patterns, the software program identifies potential downside areas earlier than they escalate. This permits producers to regulate manufacturing parameters, optimize processes, and proactively handle points earlier than defects happen.
For instance, if a manufacturing line persistently produces defects at a particular machine station, predictive analytics can pinpoint the problem and advocate corrective actions. Companies that leverage predictive analytics scale back defect charges, decrease manufacturing prices, and enhance product reliability.
3. Standardizing Manufacturing Processes with AI
Manufacturing course of management software program ensures consistency throughout manufacturing strains by monitoring gear efficiency, materials properties, and operator actions. AI-driven options regulate machine settings in actual time to take care of optimum manufacturing circumstances, decreasing variations that result in defects.
For example, if a fabric inconsistency is detected, the software program can routinely regulate machine parameters to compensate, guaranteeing that the ultimate product meets high quality requirements. Standardized processes result in fewer defects, increased manufacturing effectivity, and lowered waste.
4. Provider High quality Administration Software program
To make sure that incoming supplies meet high quality requirements, companies use provider high quality administration software program. These programs monitor provider efficiency, analyze defect charges, and implement compliance with high quality necessities. If a provider persistently delivers subpar supplies, the software program flags the problem and recommends corrective measures.
Superior provider high quality administration instruments additionally use blockchain expertise to boost traceability. By sustaining an immutable report of fabric sourcing and high quality inspections, companies can be certain that solely high-quality inputs enter manufacturing.
5. Actual-Time Defect Monitoring and Alerts
One of many greatest benefits of defect detection software program is real-time monitoring. In contrast to conventional high quality management strategies that detect defects solely on the remaining inspection stage, trendy software program options determine points as quickly as they come up in manufacturing.
IoT-enabled sensors and AI-powered cameras repeatedly analyze product dimensions, floor high quality, and useful attributes. If a deviation from acceptable parameters is detected, the system instantly sends alerts to operators and manufacturing managers. This real-time suggestions loop ensures that vital changes are made on the spot, decreasing the variety of faulty models earlier than they attain the ultimate stage.
Actual-time monitoring additionally helps in development evaluation. If a selected defect is recurring at a particular stage, producers can pinpoint the basis trigger and take corrective motion. This prevents future defects and improves total course of effectivity.
6. Root Trigger Evaluation and Course of Optimization
Discovering the basis reason behind defects is vital for long-term high quality enchancment. With out correct defect monitoring, producers might find yourself fixing signs as a substitute of the underlying downside, resulting in repeated high quality points. Defect evaluation software program makes use of AI and statistical modeling to determine patterns in manufacturing failures and hint them again to their supply.
For instance, if a producer notices {that a} specific batch of merchandise has alignment points, root trigger evaluation software program can assess varied components corresponding to machine calibration, materials consistency, and temperature variations. As soon as the primary trigger is recognized, producers can regulate machine settings, retrain staff, or modify uncooked materials specs to forestall defects from occurring once more.
Course of optimization options additionally assist producers refine manufacturing workflows. By analyzing defect frequency and placement, companies can eradicate inefficiencies and scale back pointless steps within the manufacturing course of. This results in increased productiveness, decrease defect charges, and improved profitability.
7. Digital Twin Know-how for Defect Discount
Digital twin expertise is revolutionizing high quality administration by permitting producers to create digital replicas of bodily manufacturing strains. These digital fashions simulate real-world manufacturing processes, enabling companies to check completely different eventualities and determine potential defect sources with out disrupting precise manufacturing.
With AI-driven digital twins, producers can simulate tolerance variations, analyze the impression of various machine settings, and experiment with different supplies. If a simulation reveals {that a} specific setting results in defects, changes may be made in the true manufacturing line earlier than issues come up. This predictive method minimizes manufacturing dangers, guaranteeing that solely high-quality merchandise are manufactured.
8. Customizable High quality Management Parameters
Each trade has distinctive high quality necessities, and a one-size-fits-all method doesn’t work for defect detection. Trendy high quality administration software program permits companies to set customized parameters primarily based on trade requirements, buyer necessities, and inner high quality benchmarks.
For instance, within the automotive sector, defect detection software program may be configured to evaluate components corresponding to welding precision, paint thickness, and meeting accuracy. Within the electronics trade, software program might give attention to circuit integrity, part placement, and thermal efficiency. Customizable settings be certain that producers meet regulatory compliance whereas sustaining excessive product requirements.
9. Decreasing Prices Related to Product Defects
Product defects usually are not only a high quality challenge; they’ve a direct impression on an organization’s backside line. Companies that fail to deal with defects face elevated materials prices, increased labor bills, and costly guarantee claims. Implementing software-driven defect detection considerably reduces these monetary burdens.
Materials prices lower as scrap charges go down. Since defect evaluation software program catches points early, fewer uncooked supplies are wasted on unusable merchandise. Labor prices additionally lower as a result of staff spend much less time fixing faulty merchandise or performing rework. As an alternative, they’ll give attention to core manufacturing duties, bettering total effectivity.
10. Integrating Defect Detection Software program with ERP and MES Programs
Trendy defect detection instruments are designed to work seamlessly with Enterprise Useful resource Planning (ERP) and Manufacturing Execution Programs (MES). This integration offers a complete view of manufacturing high quality, linking defect information with provide chain administration, stock monitoring, and manufacturing planning.
For instance, if defect detection software program identifies recurring points with a particular batch of uncooked supplies, ERP integration permits producers to hint the supply and notify suppliers. If a machine persistently produces faulty elements, MES integration can routinely schedule upkeep or recalibrate settings.
By integrating high quality administration software program with current manufacturing programs, companies achieve a holistic method to defect prevention. This stage of coordination reduces delays, improves decision-making, and ensures that every one departments work in direction of a standard aim of high quality excellence.
Conclusion
Product defects stay a serious problem for companies, however trendy defect detection software program offers an efficient resolution. From real-time monitoring and AI-driven high quality management to predictive analytics and digital twins, superior software program options assist producers scale back defects, enhance effectivity, and decrease manufacturing prices.
By implementing automated high quality management, companies can catch defects earlier than they attain prospects, avoiding guarantee claims and model status harm. Root trigger evaluation software program ensures that issues are completely fastened, whereas course of optimization instruments streamline manufacturing workflows. Integrating defect detection software program with ERP and MES programs additional enhances effectivity and provide chain administration.